Определение основных размеров рабочего колеса
Заданными величинами будут Q — подача; И — напор; Д/г — кавитационный запас; С — кавитационный коэффициент быстроходности. Необходимо определить диаметр рабочего колеса D; диаметр втулки dBT; густоту решетки lit (рис. 3.9) и выбрать число лопастей рабочего колеса z.
Диаметр рабочего колеса можно определить исходя из минимума потерь, используя зависимости параграфа 2.6, а также с помощью уравнения неразрывности
Из уравнения (3.12) следует, что
вводя понятие относительного диаметра втулки
Г. Ф. Проскура рекомендовал определять диаметр рабочего колеса осевого насоса, исходя из подачи, по формуле
где Q — м3/с;
п — об/мин.
Формула (3.13) получена на основании следующих рассуждений:
откуда


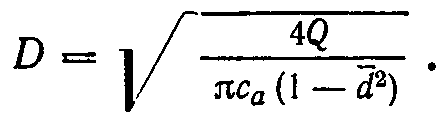

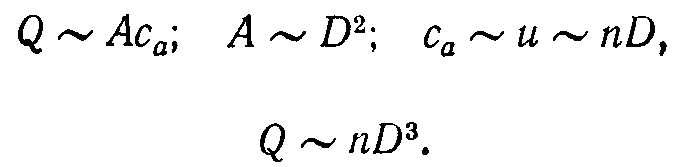
Численный, безразмерный коэффициент в формуле (3.13) — 5,0— 5,5 получен Г. Ф. Проскурой на основании обработки большого числа опытов. Как показывает практика отечественного насосостроения, окружная скорость рабочего колеса на периферийном его сечении должна быть не более 22—33 м/с, т. е. и = Ra> = 1/2nDn — 22— 33 м/с.
Диаметр втулки рабочего колеса dBT может быть вычислен, если задаться относительным диаметром втулки d, который выбирается исходя из условий приемлемой формы корневого сечения лопасти. Оптимальное значение d в каждом отдельном случае устанавливают из опыта.
С уменьшением радиуса рабочего колеса растут углы установки профиля 0, а также его кривизна. Предпочтительнее диаметр втулки уменьшить, но его уменьшение лимитируется максимальными углами установки профиля и возможностью размещения во втулке механизма поворота лопастей.
Численные значения втулочного отношения d = 0,4—0,6. Чем больше коэффициент быстроходности, тем эта величина будет меньше *. Приведенные значения соответствуют углам установки профиля: р = 35—38°.
Густота решетки l/t также, как и d, выбирается на основании опытных данных. Рекомендуется l/t от втулки к наружному диаметру уменьшать. У втулки принимают l/t в 1,25—1,30 раза больше, чем у наружного диаметра колеса, что позволяет последнему быть более прочным. Обычно lit — 0,6—1,0.
Выбор (///)пер периферийного сечения можно производить по графикам, полученным на основании опытов [11].
Число лопастей рабочего колеса г существенно влияет на величину создаваемого напора и зависимости Н — Q и ц — Q. Выбор числа лопастей тесно связан с густотой решетки l/t. Увеличение числа лопастей приводит к уменьшению шага, а следовательно, и к увеличению напора.
В таблице 3.1 показана взаимосвязь между:
d — относительным диаметром втулки;
zpK — числом лопастей рабочего колеса;
zBa — числом лопастей выправляющего аппарата?
Итак — максимальным напором и коэффициентом быстроходности ns.
На рис. 8.18 приведены данные испытаний насоса с одинаковыми лопастями при их числе от двух до пяти. После определения основных размеров приступают к профилированию лопастей. Лопасти рассчитывают по цилиндрическим сечениям, беря для этого 5—8 сечений (рис. 3.19).
Существует несколько методов профилирования (расчета) лопастей.
Метод расчета с использованием треугольников скоростей — уравнения (3.5), (3.6) — и коэффициента подъемной силы Су — урав-
Таблица 3.1
Величины |
ns |
||||
400 |
600 |
800 |
1000 |
1200 |
|
т |
0,6 |
0,55 |
0,50 |
0,45 |
0,40 |
6 |
5 |
4 |
3 |
2 |
|
?ва |
9 |
9 |
7 |
5 |
5 |
LT лтях |
2Б |
15 |
10 |
6 |
‘ 3 |
нения (3.9), (3.11) — носит название метода подъемных сил. Расчет в этом случае сводится к подбору профилей решетки (по известным параметрам треугольников скоростей и коэффициентам подъемной силы). Для этой цели используются соответствующие атласы профилей. Нужно иметь в виду, что коэффициент
подъемной силы Су изолированного (одиночного) профиля не всегда будет равен коэффициенту подъемной силы того же профиля в решетке Сур. Сказывается влияние профилей друг на друга. Для низконапорных насосов, когда густота решетки l/t^. 1 можно принять Су = Сур- В остальных случаях необходимо, пользуясь графиками [20], найти поправочный коэффициент/, = f (Т, 0) и тогда Сур = LCU. Метод подъемных сил сравнительно прост, но отсутствие четких рекомендаций по выбору Су, Сх и X ограничивает его применение.
Одним из совершенных способов профилирования лопастей осевых
машин является метод интегральных уравнений, предложенный в 30-х гг. И. Н. Вознесенским и В. Ф. Пекиным. В дальнейшем этот метод усовершенствован Н. А. Колокольцевым, А. Ф. Лесохиным, Л. А. Симоновым и др. [11; 20]. С помощью метода интегральных уравнений по заданным характеристикам потока определяют геометрические параметры решетки. Суть его состоит в том, что действительная решетка профилей заменяется эквивалентной решеткой, состоящей из бесконечно тонких дужек. Далее составляются и решаются уравнения обтекания дужек с заменой последних вихревой поверхностью, после чего дужки «одеваются» соответствующими телесными профилями.

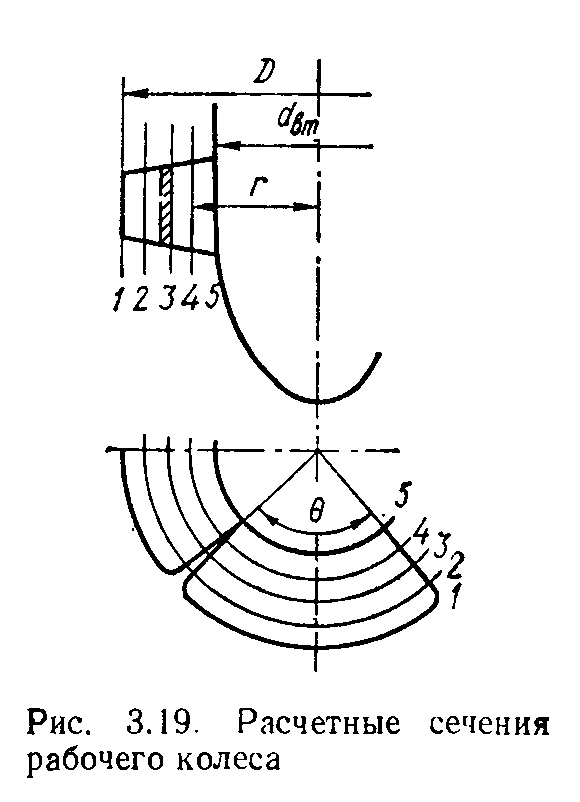